Initially, two bearings were tested to see if they could spin two sections independently. The bearings worked well but they needed to be tested on a larger scale with the correct materials.
This method was then tested on a plywood prototype that had the betting area design laser cut into it. Since the design at this stage required the two sections of the wheel to be flush, this prototype helped to inform the design of future prototypes.
The above photograph shows the bearing system used within the first full-sized prototype. The nuts act as washers for the bearings.
The holes next to it are of different sizes and were used to test the tolerances of the laser-cutter when getting a perfect fit around the bearing’s edge.
This system was then tested at a larger scale within an actual table. However, to do this, a hole had to be cut out of the table. Since the table did not fit within the CNC bed, the hole was cut by hand using a jigsaw and a template router.




The spindle was then screwed into the base plate and two separate sections were attached to the spindle.
Although the spindle was partially successful, it allowed for the two sections to wobble. This is due to the bearings having a very small surface area in comparison to the wheels. Future iterations require larger bearings and a more secure spindle. The wheels also kept spinning for a very long time, showing that the friction of the bearings needs to be considered.

To reduce the wobble of the sections, ball transfer units (ball rollers) were used. Although this massively reduced the wobble whilst spinning the wheel, the noise that they created was very loud. Since one of the specifications of the project is to deactivate users, a new way of solving the wobble needed to be explored.

Since this did not work, another method of reducing the wobble was used. This included using larger bearings and a wider central axle.
_________________________________________________________________________
COVID-19 LOCKDOWN BEGAN
_________________________________________________________________________
Due to the lockdown, access to facilities needed to continue physically prototyping the mechanism were unavailable. However, the previous iteration of the mechanism was close to being completed and with the aid of some secondary research, a mechanism was designed that, in theory, works successfully.
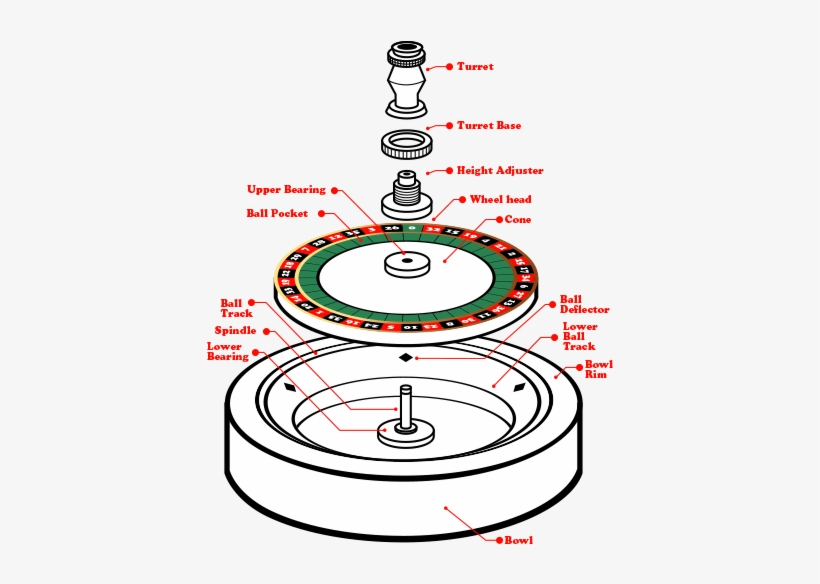
Existing roulette wheels use a spindle and two bearings both above and below the rotating wheel head to stop it from wobbling. The spindle is also connected to a base plate.
This approach was therefore taken forward. Three bearings would now be used; one bearing for the smaller, top section of the wheel and two bearings for the larger, bottom section of the wheel. This can be seen below.

The spindle was now fully resolved and through defining the specific sizes and tolerances of the various elements, the spindle should prevent any wobbling from occurring whilst spinning.
The tolerance of the bearings and the conical sections provide a tight fit, allowing for the wheel to be perfectly horizontal whilst spinning.
Tiny washers are used to separate each section, reducing friction. This allows the product to meet the product design specification as it does not create any noise whilst spinning.
Technical implications
The smaller the gap is between the base plate, the bottom cone and the top cone, the more visually appealing the wheel is. However, if the gap is too small, then there is a greater possibility that the sections will touch each other whilst spinning. This would be tested and if the sections did touch, the gap between the sections would be increased.